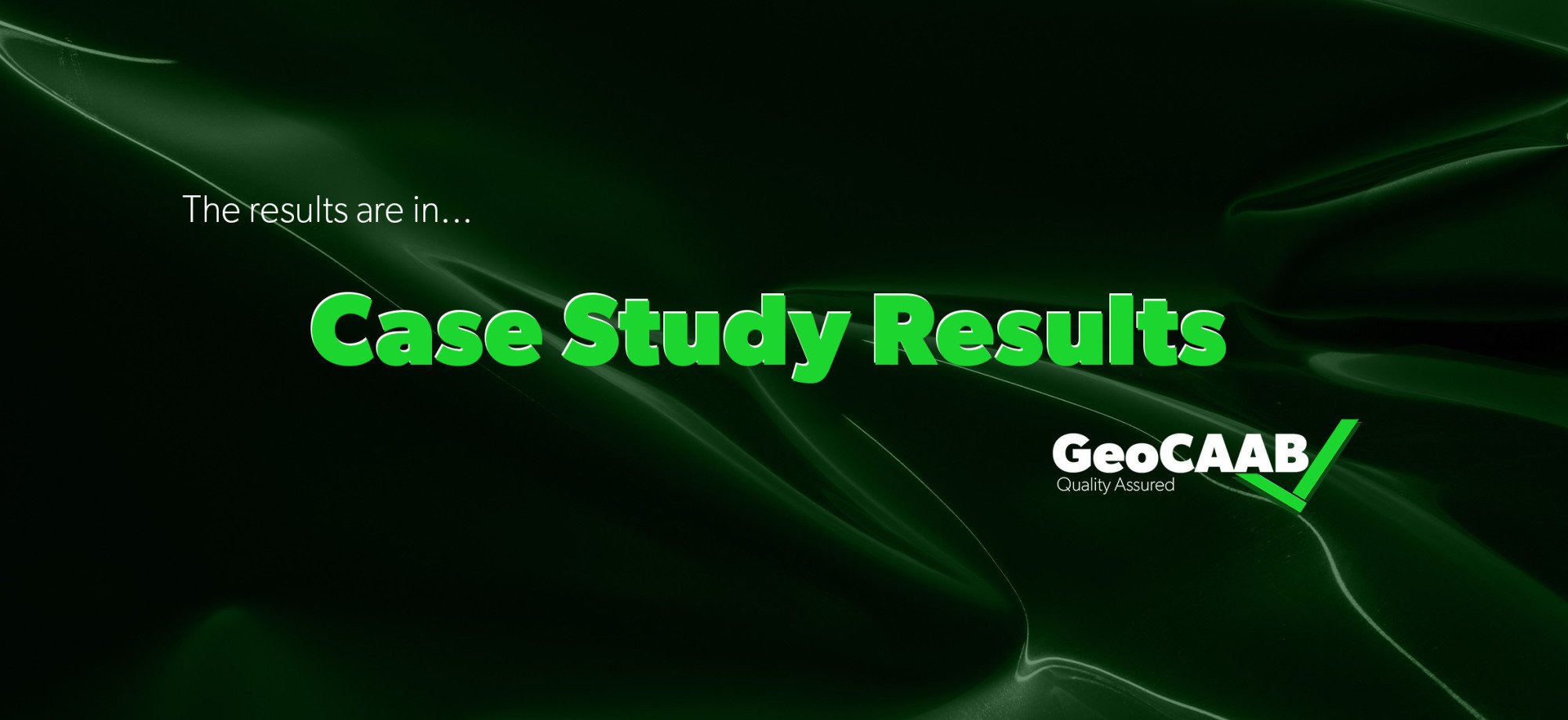
Table of Contents
The results are in!
Our latest Case Study indicates that GeoCAAB optimizes time, labor, money, and quality, unlike any other quality control method in the geosynthetics industry. Results show that no other process can replicate the efficiency, cost savings, and accuracy that managers, owners, and stakeholders experience using GeoCAAB.
71% FASTER data collection
Our research shows that even a QA/QC Tech with one year of experience can complete their documentation 70.83% faster than a QA/QC Tech with 15 years of experience using traditional, manual methods. (Reference Case Study 1 below.)
Now, we understand if you want more reassurance than one isolated case study can provide before switching to automated quality control. That's why we gathered and analyzed 20 years of data to substantiate our findings.
178% more projects and 74% less time spent per project
Records indicate that employees using Geocaab worked on 178 % more projects and spent 73.68% less time per project than employees who didn't use GeoCAAB. Additionally, there is a staggering 85.17% reduction in overtime hours using GeoCAAB, potentially leading to significant cost savings. (Reference Case Study 2 below.)
The Bottom Line: GeoCAAB Makes Sense
With GeoCAAB, you get more than just software. You get:
- Reduced Costs: Save money on labor, overtime, and rework due to manual errors.
- Improved Accuracy: Eliminate data entry errors and ensure consistent, reliable records.
- Increased Efficiency: Free your team to focus on critical tasks and complete more projects.
Ready to ditch the paperwork and embrace a new era of efficiency? Contact us today and see how GeoCAAB can revolutionize your geosynthetics QA/QC.
GeoCAAB: Experience the Next Revolution in Geosynthetics
We are a computer-aided as-built software, built by the field, for the field, that utilizes GPS mapping to maximize efficiency, accuracy, and organization.
LinkedIn | Facebook | Instagram | Twitter | Youtube
Subscribe to our Blog | (1 (888) 401-5196 )
References:
Case Study 1: Our first study involved two QA/QC Technicians, each with a different experience level, collecting and inputting data on a 15,000 SF area. We compared the time it took an experienced QA/QC Tech to manually collect and input their data to the time it took a new QA/QC Tech to do the same using GeoCAAB. The QA/QC Technician with 15 years of experience spent 6 hours drawing the as-built and manually inputting data. The QA/QC Technician with one year of experience spent 1 hour and 45 minutes accomplishing the same using GeoCAAB. The less experienced QA/QC Tech could complete his work in 70.83% less time than the more experienced QA/QC Tech using traditional methods.
Case Study 2: Our second case study compares results from employees who didn't use GeoCAAB to those who did use GeoCAAB over an extended period. During eight years of employment, two QA/QC Techs who weren't using GeoCAAB spent 9,472 hours across 293 projects. 1,079 of these hours were overtime hours. That's an average of 32.3 hours per project for each employee. In comparison, two QA/QC Techs who used GeoCAAB for 12 years spent 6,858 hours across 815 projects. Only 160 of those hours were overtime hours. That's an average of 8.5 hours per project for each of the two employees. In conclusion, over 12 years, employees using Geocaab worked on 178% more projects and spent 73.68% less time per project than employees who didn't use GeoCAAB for eight years. Additionally, there was an 85.17% reduction in overtime hours using GeoCAAB, potentially leading to significant cost savings.